AIが生みだす新構造 x ヒトが考えるデザイン
G-SHOCK 40TH ANNIVERSARY MODEL「G-D001」
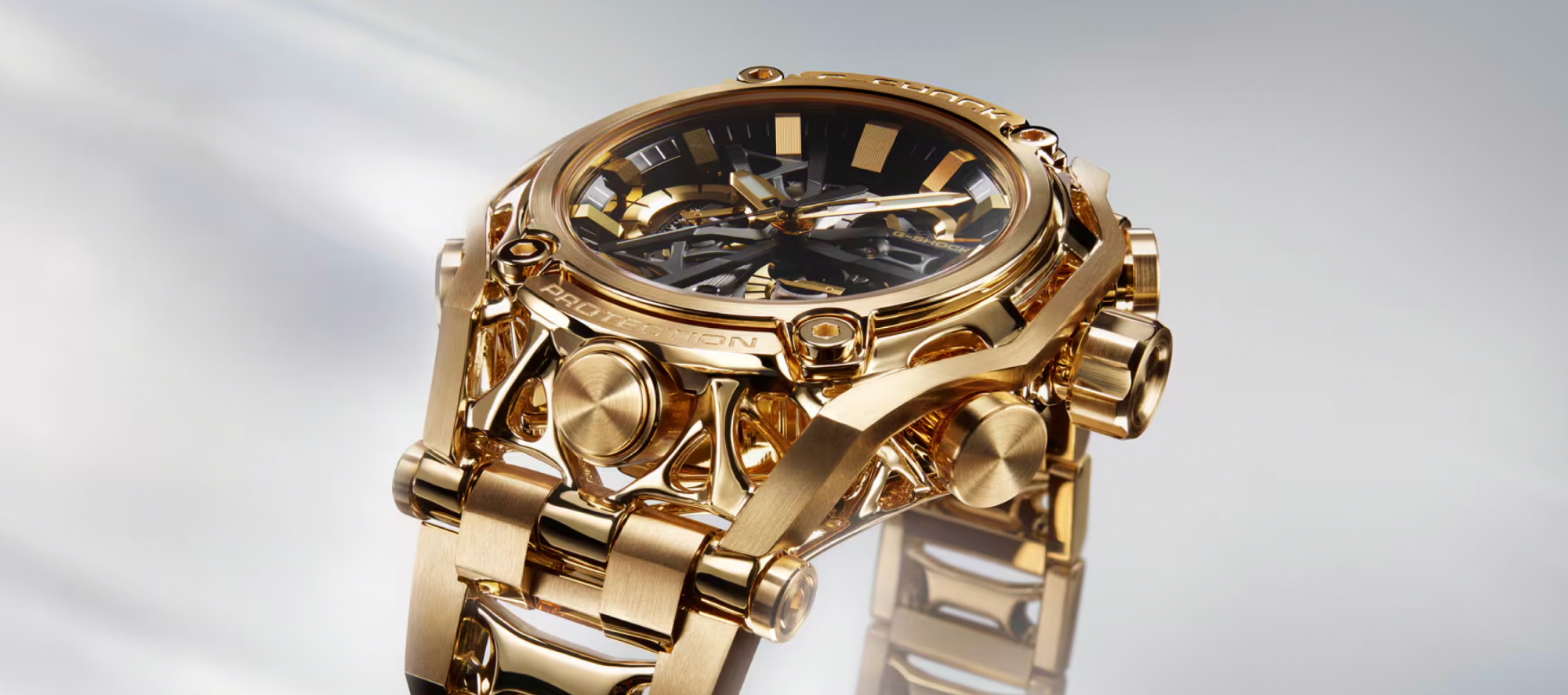
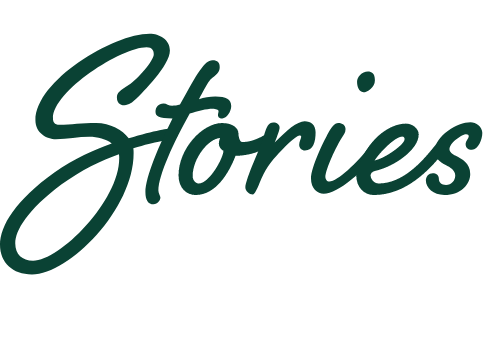
新たな手法で 世界に1本しかないデザインを手がけることに!
グローバルで人気の「G-SHOCK」は2023年に40周年を迎え、
企画されたその記念モデルの誕生にはどんなプロセスがあったのか。
プロダクトデザインを担当したリョウさんに語っていただきます。ここでしか見ることができない写真は必見!

AIを使ったデザイン開発
僕の研究テーマとして、デザイン・外装設計の可能性を模索する目的で、ジェネレーティブデザインを長く1人で研究していました。いわゆるAIの活用です。
G-SHOCKの画期的な耐衝撃構造は「3階のトイレから時計を落としてみる」という大先輩の地道な実験で生まれましたが、AIを導入すればさらに進化できると思ったのです。
具体的には、ケース内でモジュールを浮かせたり緩衝材を挟んだりする従来の手法ではなく、ケースそのものに衝撃吸収性を備えさせたいと考え、「この方向からは何ニュートンの力に耐えてほしいか?」といったデータを割り出すところからスタートしました。
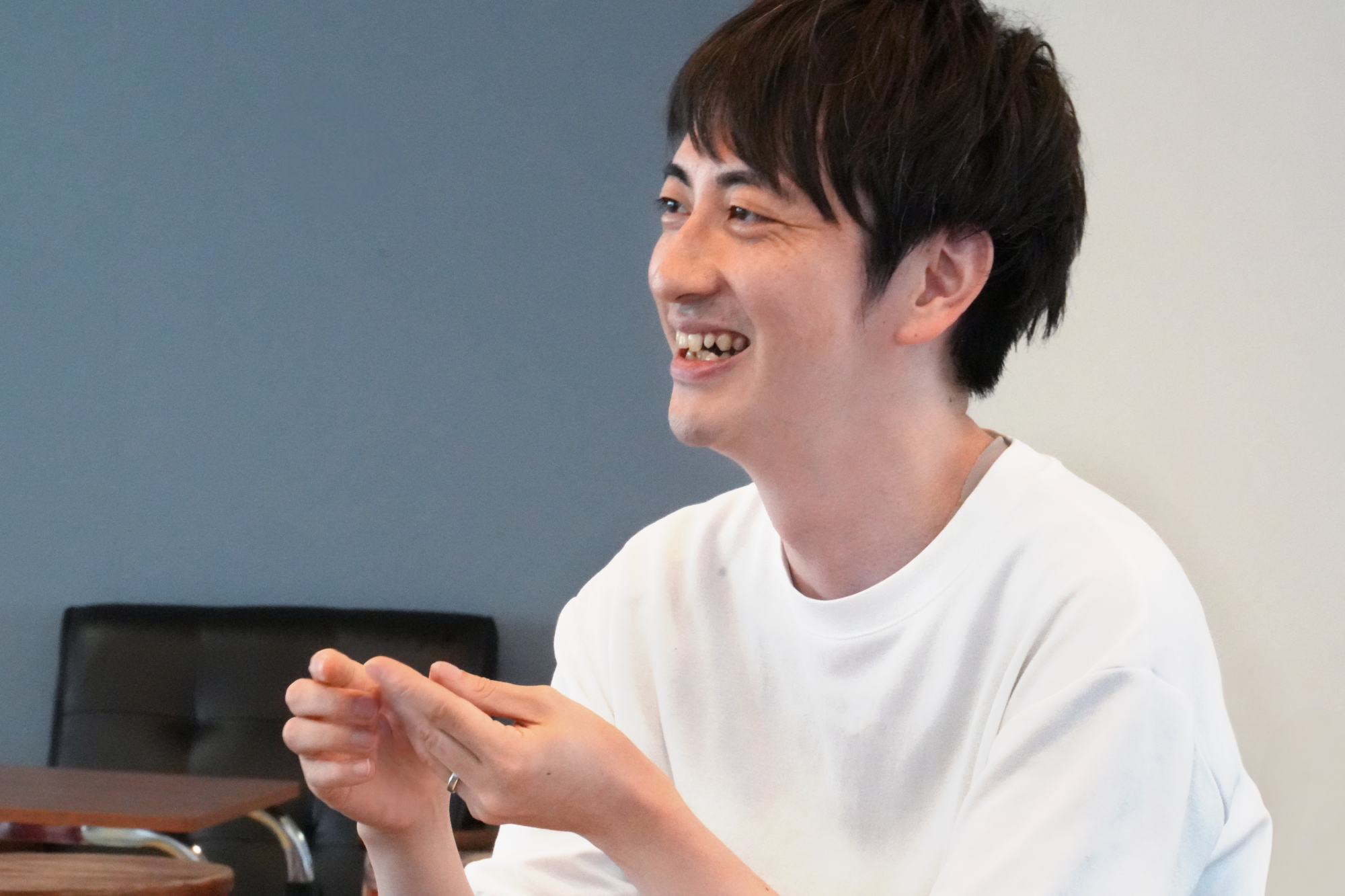
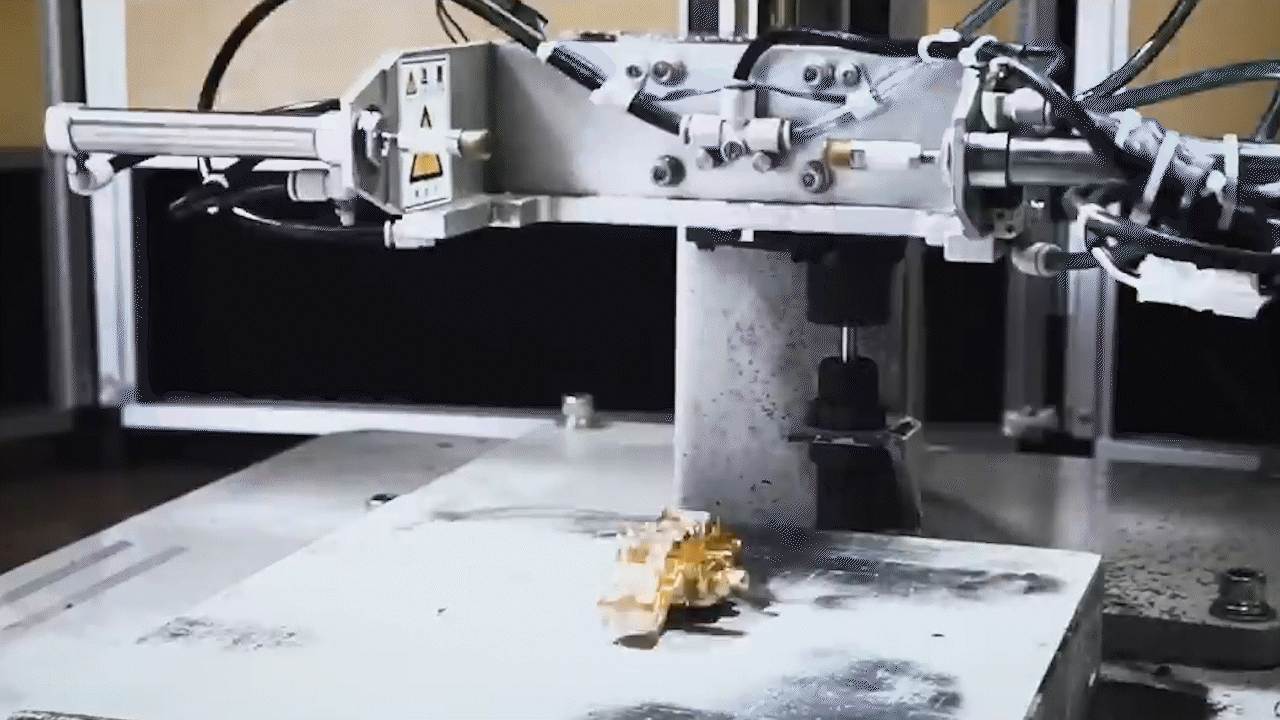
18K素材で実証テストを複数回実施
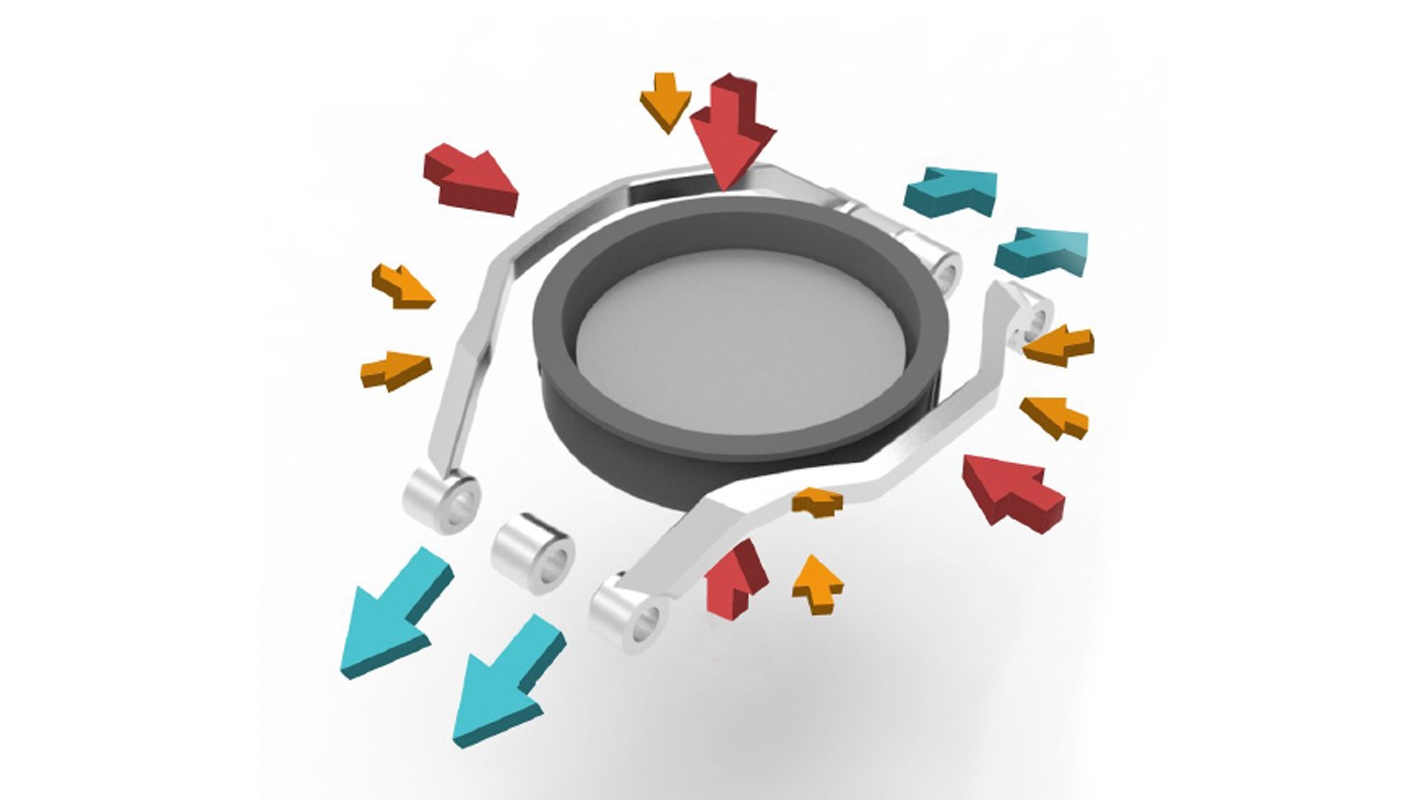
時計に加わる衝撃のデータを入力
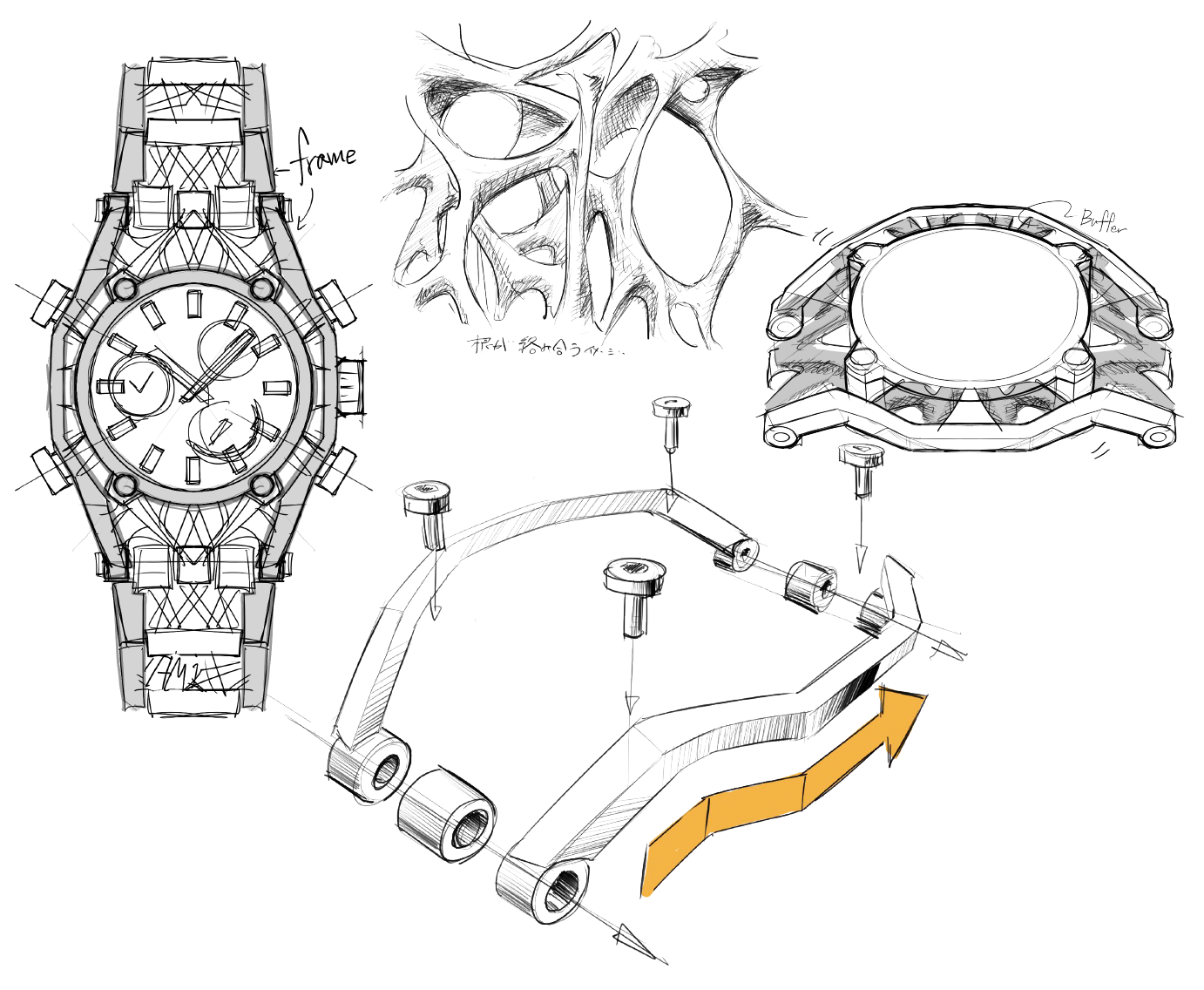
初期に描いたデザインスケッチ

AIとデザイナーの役割
AIだからといって、ボタンひとつですばらしい結果が出てくるわけではありません。AIに任せっきりだと、時計として機能しないデザインが出てきてしまうのです。
そのため、大切にしたのは“人とAIの共創”です。これまで40年間培ってきた耐衝撃設計のノウハウを数値化しAIで計算させ、定義した条件を基に最適な形状をはじき出してくれる。一方で、自然界特有の力強い動物の骨格や植物をモチーフにした有機的な構造は僕がイメージしたものです。
AIが計算した形状をイメージに合わせて修正したりそれをまた計算させたりと、デザイナーとAIがアイデアを行き来し作り上げるプロセスこそが”共創”でした。AIと一緒にデザインを突き詰めていくことによって、G-D001の独創的な外装構造が完成したんです。
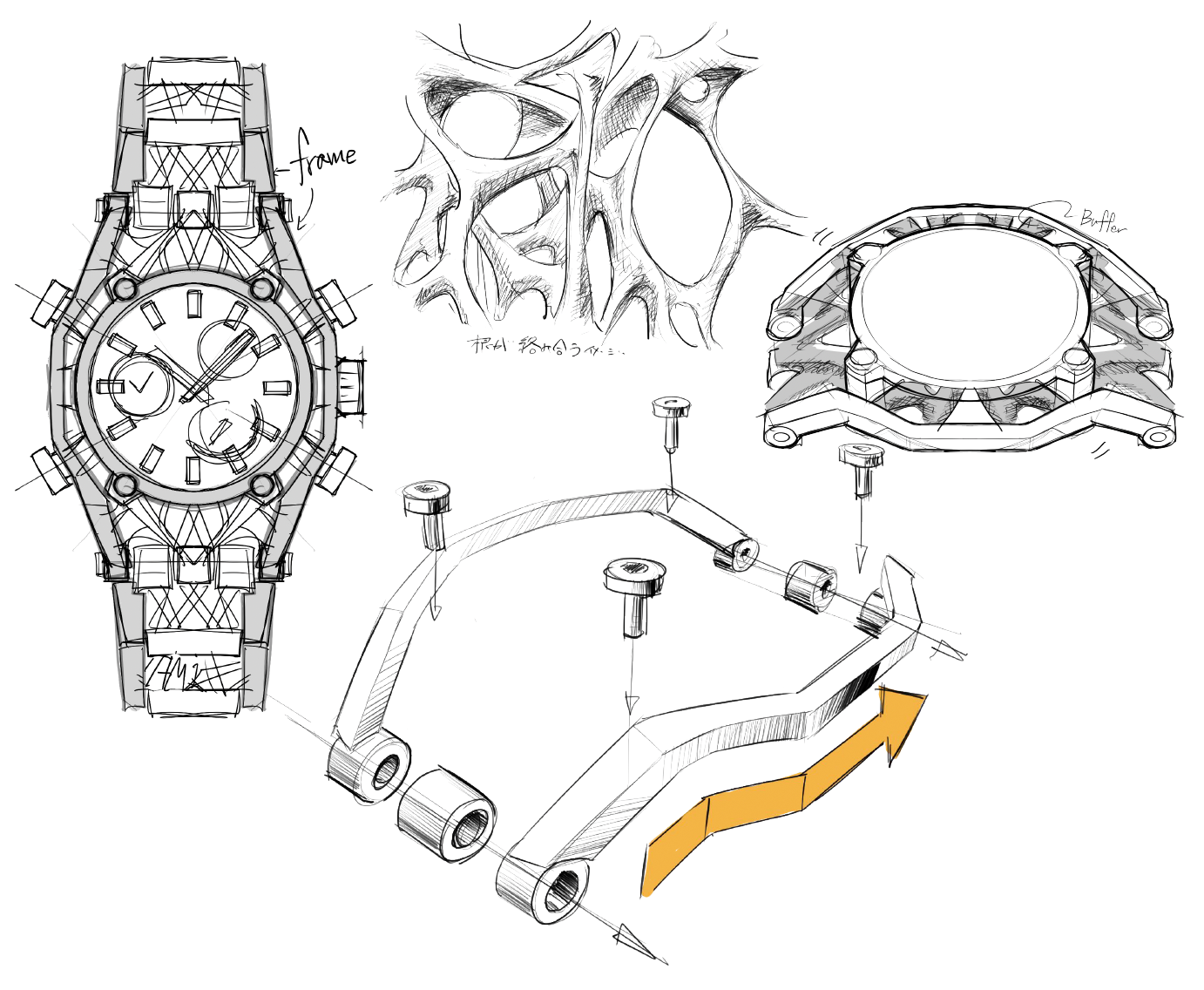

AIの活用により、人の手だけでは作り出せないユニークなデザインを生み出すことができました。
と同時に、従来の製法では加工ができないという新たな問題も出てきました。
ロストワックス製法
最終的にたどり着いたのは、G-SHOCKでは活用したことのなかったロストワックス製法でした。
この方法は、指輪などアクセサリーを作る際に多用されている鋳造技術です。これならG-D001の精巧なケースを作れると考えたからです。3Dプリンターで精巧な模型を作った後に鋳型を作るのですが、時計のケースほどの大きさで、G-SHOCKが求める寸法精度を実現するには非常に困難でした。しかし何度も試行錯誤を繰り返した結果、ついに実現することができました。
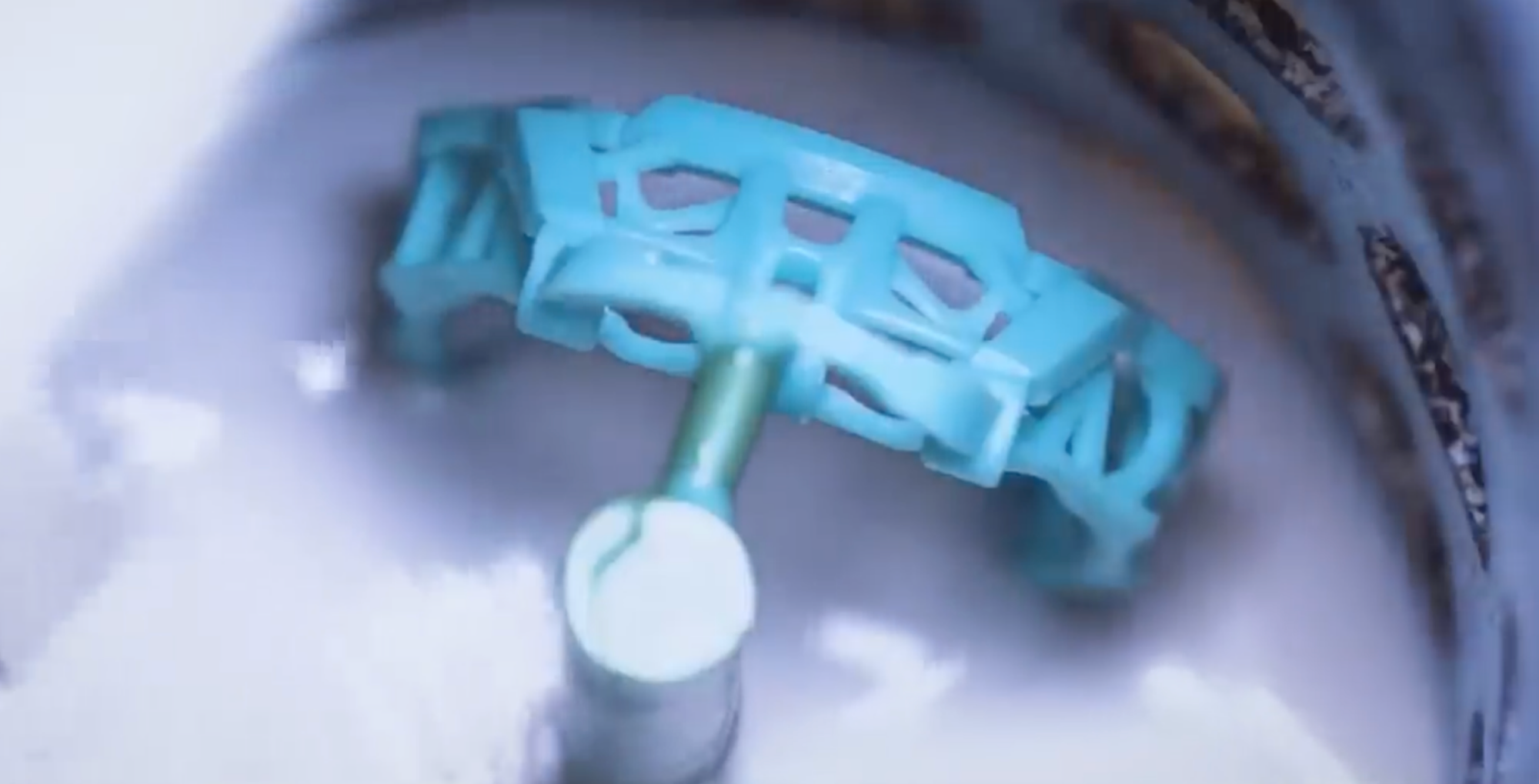
ロストワックス製法
匠の研磨職による磨き上げ
このデザインはあまりにも精緻な構造をしているため、これまでのように機械を使った仕上げ作業を行うこともできませんでした。そのため、リューターや糸状の研磨機などジュエリー製造で用いられる道具を使い、熟練の職人の手によって丁寧に仕上げてもらっています。

研磨職人の手による磨き上げ
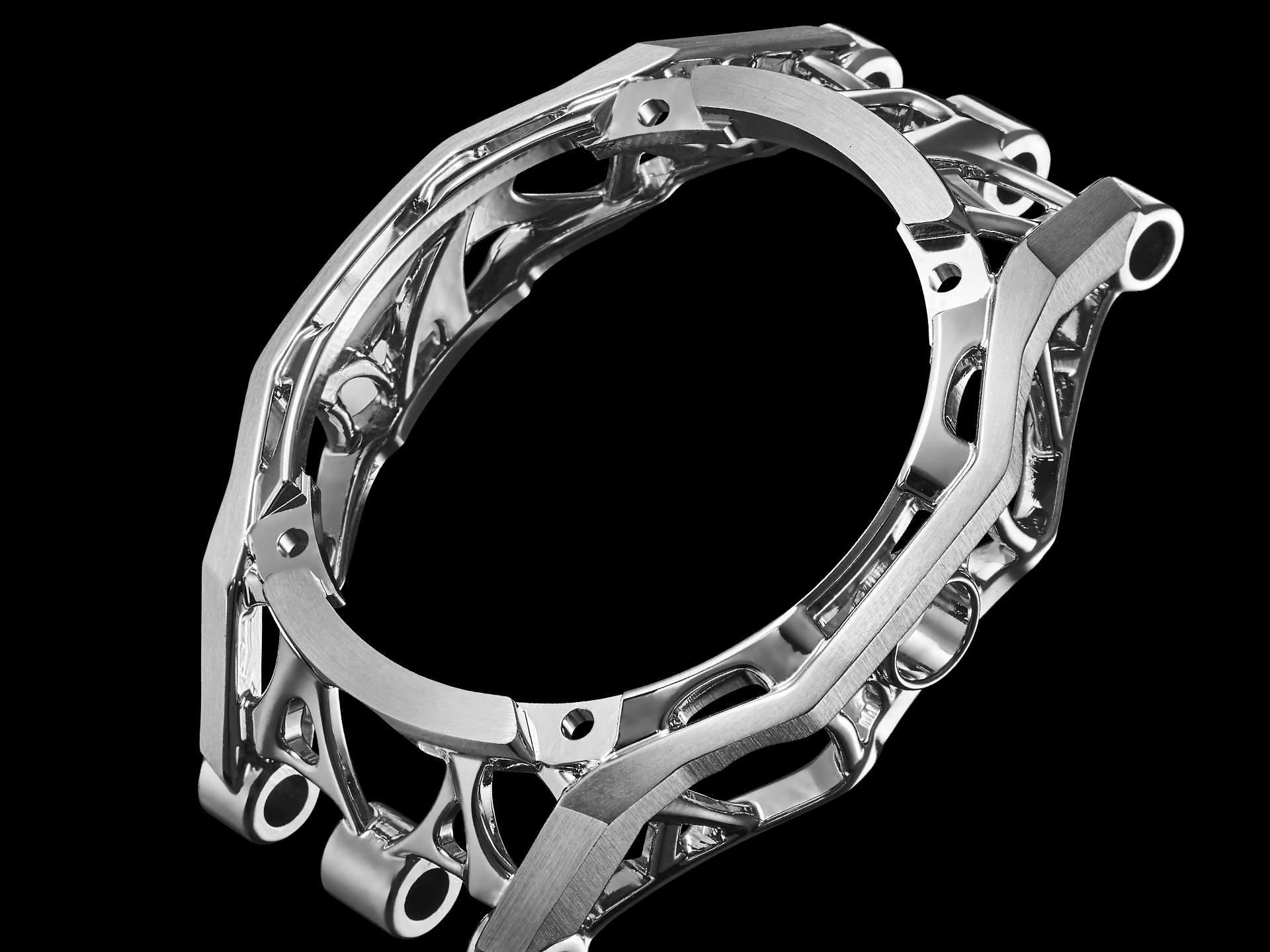
ダミーを作成して検証を繰り返したケース
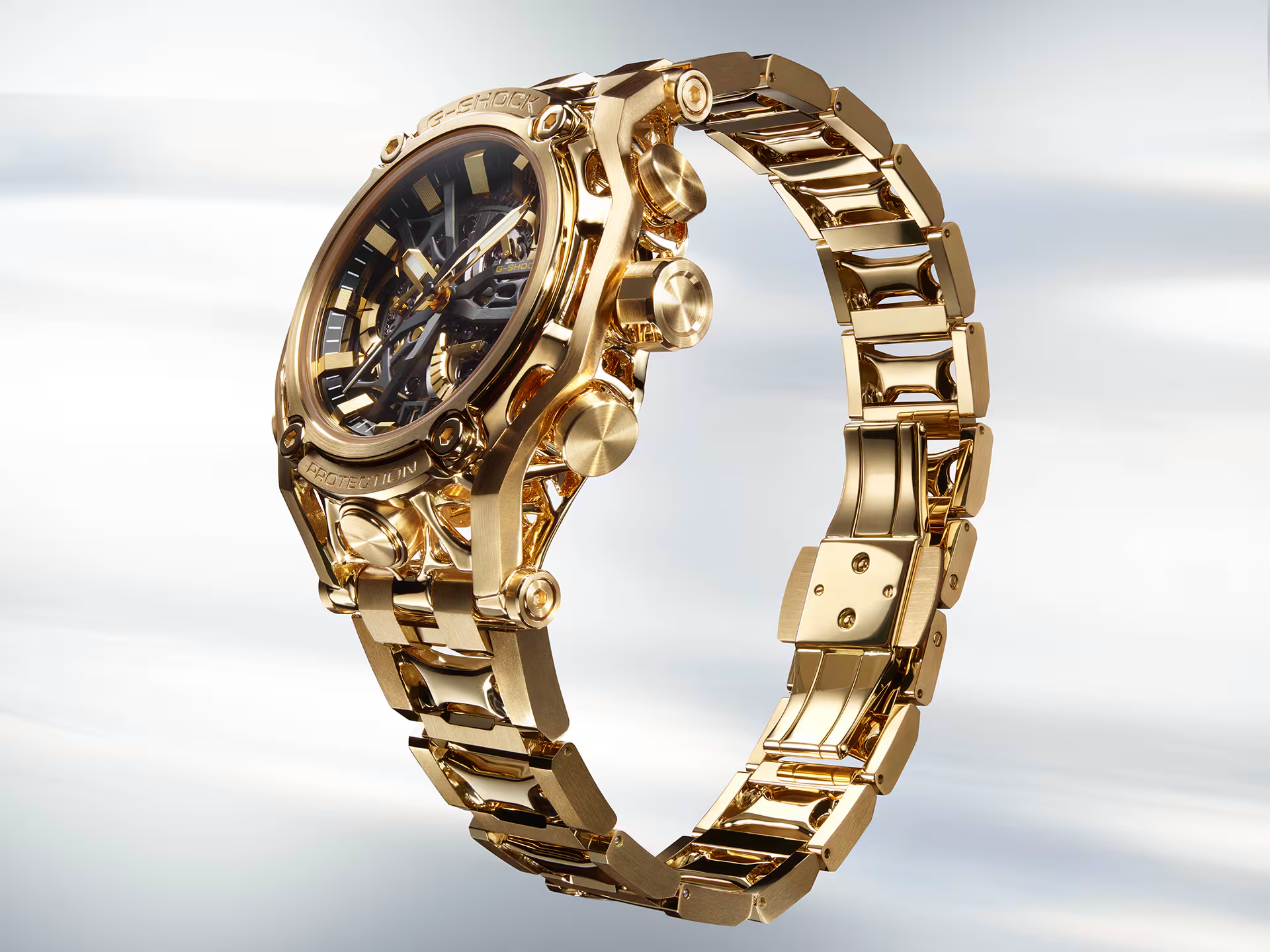
加工や磨きなど克服すべき課題が多く見つかったものの、AIを活用することで人間だけでは出来なかった独創的なスタイルを実現できたと思います。
デザイナーとして非常に刺激的で、大きな実りを感じたプロジェクトでした。AIとの共創を図るジェネレーティブデザインは、大いなる可能性を秘めています。
可視化された音の流れが、
プレイヤーの感性を刺激する
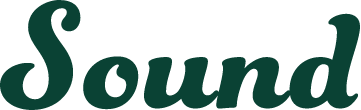
CASIO独自のHorizontal Bass-Reflex System(*1)によって実現した、高音質でありながらコンパクトなボディという
「CT-S1000V」の特徴。
これをデザインで表現するという課題もまた、難関のひとつでした。
そこで着目したのが、パンチングネット部分です。
プレイヤーが調整しながら生み出した音源が、アンプからスピーカーに送られ、音として流れる動きを、造形によって視覚的に再現。
さらに所有欲を刺激するため、パンチングネット越しに配置された大胆なCasiotoneのロゴや、緻密な立体造形にもこだわり、デザインが完成しました。